Pilihan rawatan permukaan adalah masalah yang dihadapi setiap pereka. Terdapat banyak jenis pilihan rawatan permukaan yang tersedia, dan pereka peringkat tinggi bukan sahaja harus mempertimbangkan ekonomi dan kepraktisan reka bentuk, tetapi juga memberi perhatian kepada proses pemasangan dan juga keperluan alam sekitar. Berikut adalah pengenalan ringkas kepada beberapa lapisan yang biasa digunakan untuk pengikat berdasarkan prinsip -prinsip di atas, untuk rujukan oleh pengamal pengikat.
1. Electrogalvanizing
Zink adalah salutan yang paling biasa digunakan untuk pengikat komersial. Harga agak murah, dan penampilannya baik. Warna umum termasuk hijau hitam dan tentera. Walau bagaimanapun, prestasi anti-karatnya adalah purata, dan prestasi anti-karatnya adalah yang paling rendah di kalangan lapisan penyaduran zink (salutan). Secara amnya, ujian semburan garam neutral keluli tergalvani dilakukan dalam masa 72 jam, dan ejen pengedap khas juga digunakan untuk memastikan ujian semburan garam neutral berlangsung selama lebih dari 200 jam. Walau bagaimanapun, harganya mahal, iaitu 5-8 kali dari keluli tergalvani biasa.
Proses electrogalvanizing terdedah kepada pelengkap hidrogen, jadi bolt di atas gred 10.9 umumnya tidak dirawat dengan galvanizing. Walaupun hidrogen boleh dikeluarkan menggunakan ketuhar selepas penyaduran, filem passivation akan rosak pada suhu di atas 60 ℃, jadi penyingkiran hidrogen mesti dilakukan selepas elektroplating dan sebelum passivation. Ini mempunyai operasi yang lemah dan kos pemprosesan yang tinggi. Pada hakikatnya, loji pengeluaran umum tidak secara aktif mengeluarkan hidrogen kecuali diberi mandat oleh pelanggan tertentu.
Konsistensi antara tork dan daya pengetatan pra pengikat galvanized adalah miskin dan tidak stabil, dan mereka umumnya tidak digunakan untuk menghubungkan bahagian -bahagian penting. Untuk meningkatkan konsistensi tork preload, kaedah bahan pelincir salutan selepas penyaduran juga boleh digunakan untuk memperbaiki dan meningkatkan konsistensi preload tork.
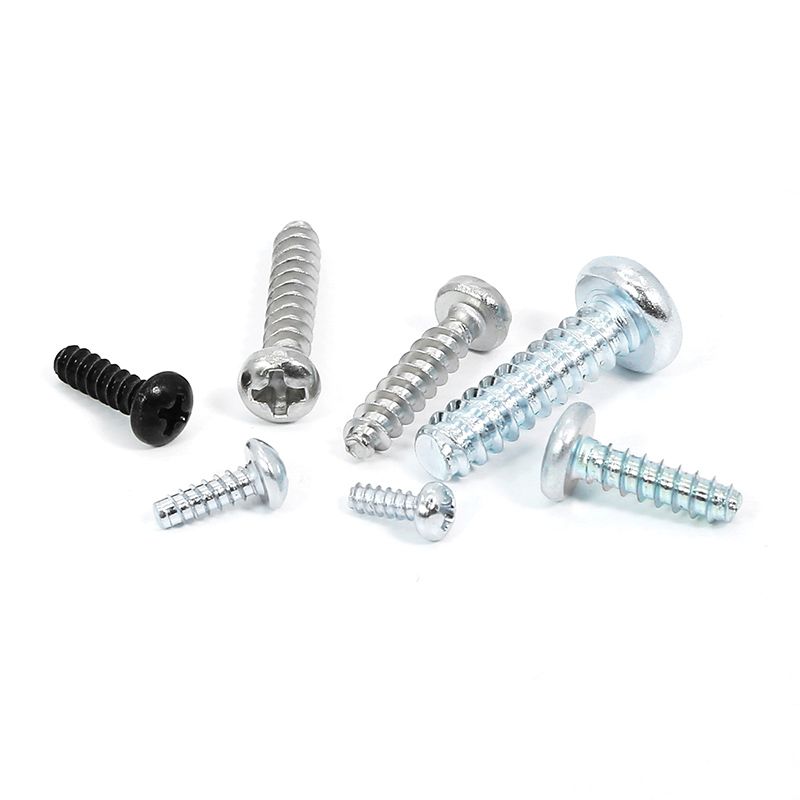
2. Fosfat
Prinsip asas adalah bahawa fosfat adalah lebih murah daripada galvanizing, tetapi rintangan kakisannya lebih buruk daripada galvanizing. Selepas fosfat, minyak perlu digunakan, dan rintangan kakisannya berkait rapat dengan prestasi minyak yang digunakan. Sebagai contoh, selepas fosfat, memohon minyak anti karat umum dan menjalankan ujian semburan garam neutral hanya 10-20 jam. Memohon minyak anti karat bermutu tinggi boleh mengambil masa sehingga 72-96 jam. Tetapi harganya adalah 2-3 kali dari minyak fosfat umum.
Terdapat dua jenis fosfat yang biasa digunakan untuk pengikat, fosfat berasaskan zink dan fosfat berasaskan mangan. Fosfat berasaskan zink mempunyai prestasi pelinciran yang lebih baik daripada fosfat berasaskan mangan, dan fosfat berasaskan mangan mempunyai rintangan kakisan yang lebih baik dan rintangan haus daripada penyaduran zink. Ia boleh digunakan pada suhu antara 225 hingga 400 darjah Fahrenheit (107-204 ℃). Terutamanya untuk sambungan beberapa komponen penting. Seperti menghubungkan bolt rod dan kacang enjin, kepala silinder, galas utama, bolt roda roda, bolt roda dan kacang, dll.
Bolt kekuatan tinggi menggunakan fosfat, yang juga boleh mengelakkan isu -isu pelindung hidrogen. Oleh itu, bolt di atas gred 10.9 dalam bidang perindustrian umumnya menggunakan rawatan permukaan fosfat.
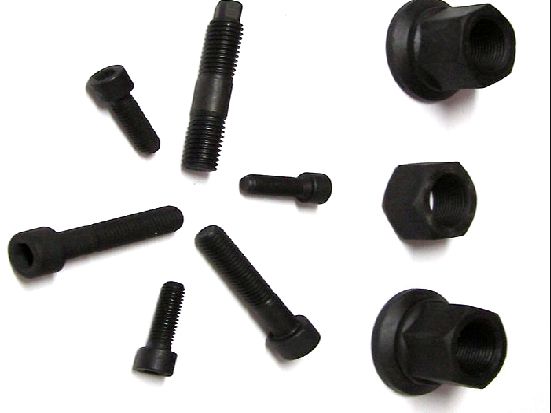
3. Pengoksidaan (Blackening)
Blackening+Oiling adalah salutan yang popular untuk pengikat industri kerana ia adalah yang paling murah dan kelihatan baik sebelum penggunaan bahan api. Oleh kerana pengikatannya, ia hampir tidak mempunyai keupayaan pencegahan karat, jadi ia akan berkarat dengan cepat tanpa minyak. Malah di hadapan minyak, ujian semburan garam hanya boleh berlangsung selama 3-5 jam.
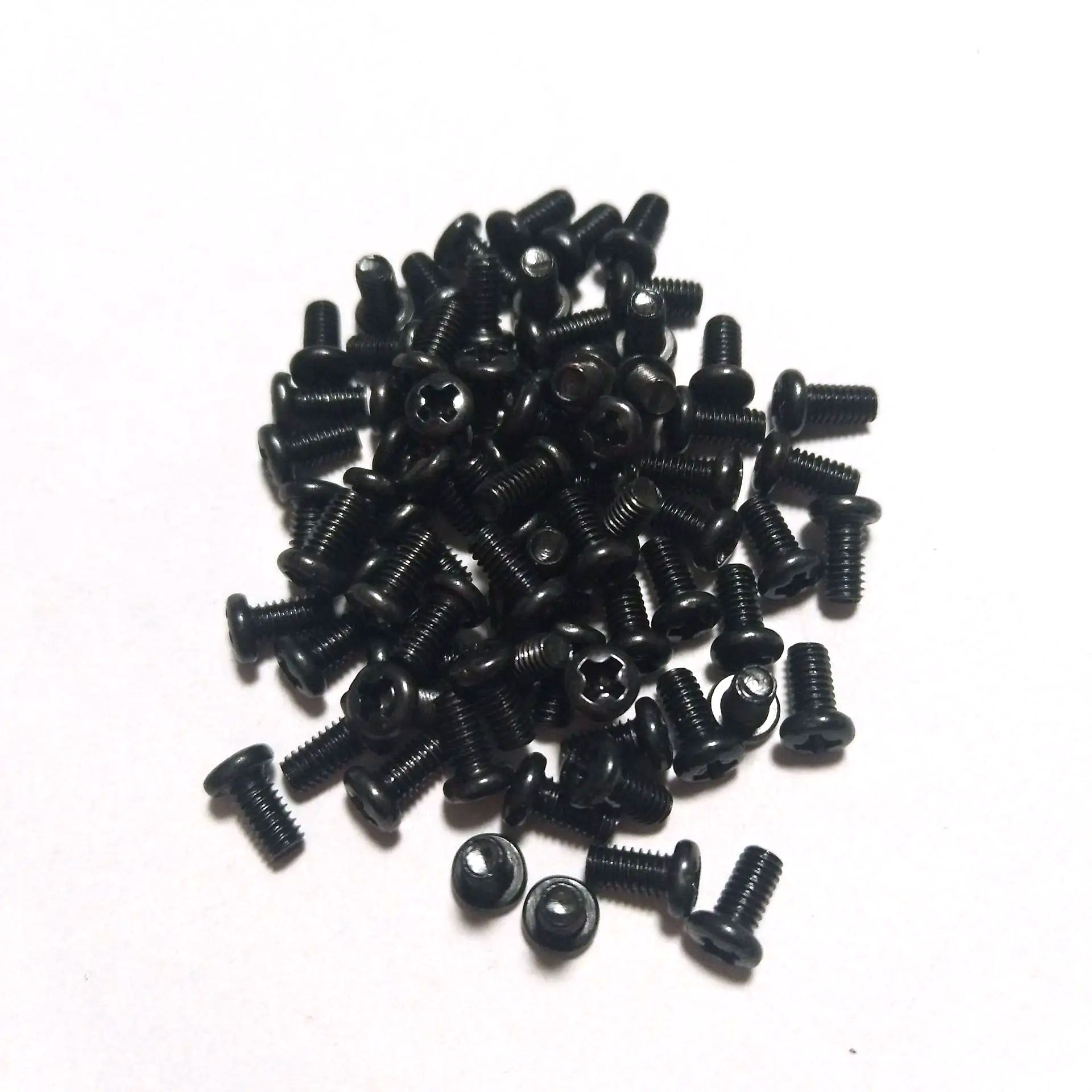
4. Partition Electroplating
Penyaduran kadmium mempunyai rintangan kakisan yang sangat baik, terutamanya dalam persekitaran atmosfera marin, berbanding dengan rawatan permukaan yang lain. Kos rawatan cecair sisa dalam proses elektroplating kadmium adalah tinggi, dan harganya adalah kira-kira 15-20 kali daripada zink elektroplating. Jadi ia tidak digunakan dalam industri umum, hanya untuk persekitaran tertentu. Pengikat yang digunakan untuk platform penggerudian minyak dan pesawat HNA.
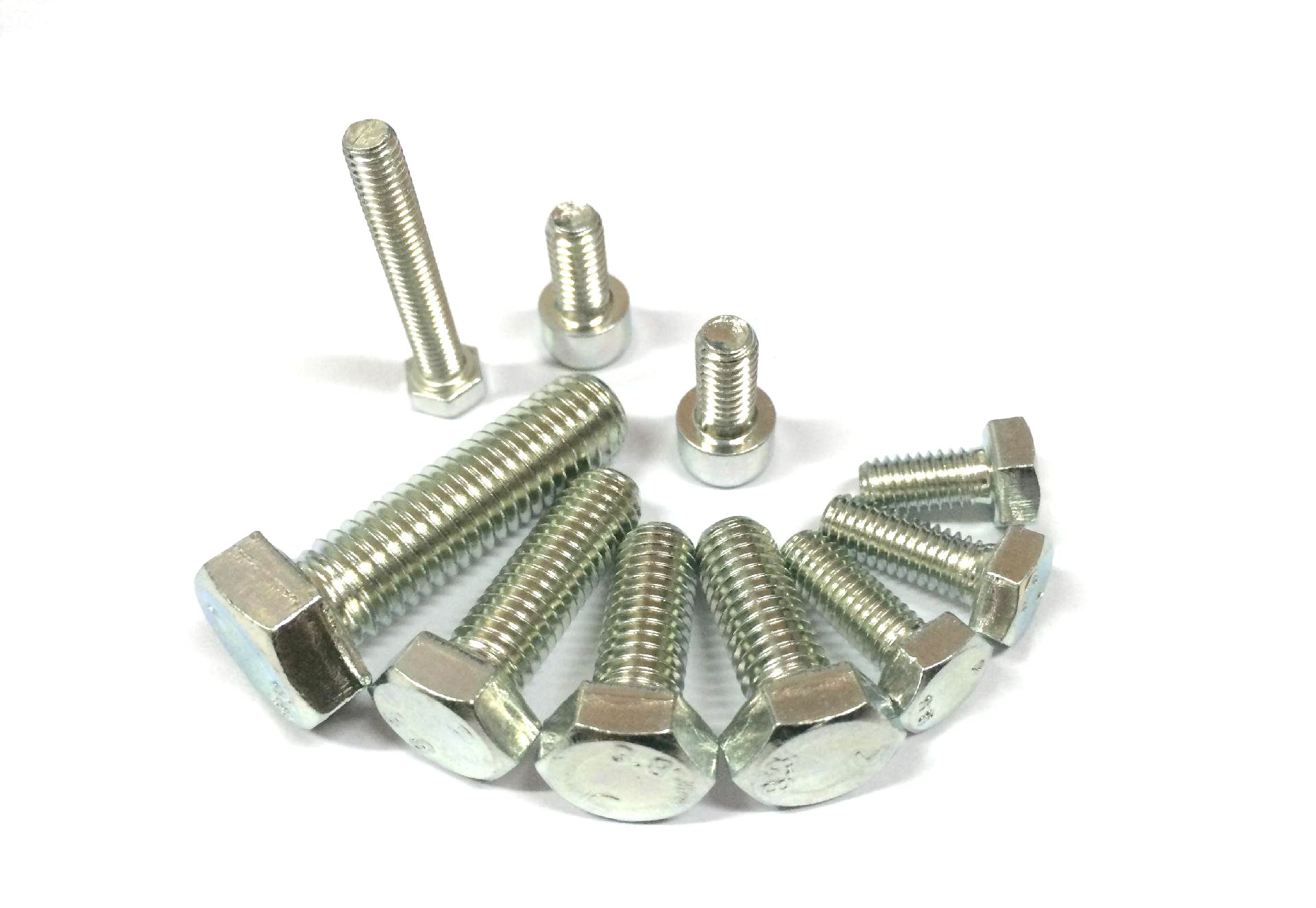
5. PLATING CHROMIUM
Lapisan kromium sangat stabil di atmosfera, tidak mudah untuk mengubah warna dan kehilangan kilauan, dan mempunyai kekerasan yang tinggi dan rintangan memakai yang baik. Penggunaan penyaduran kromium pada pengikat biasanya digunakan untuk tujuan hiasan. Ia jarang digunakan dalam bidang perindustrian dengan keperluan rintangan kakisan yang tinggi, kerana pengikat bersalut krom yang baik adalah sama mahal seperti keluli tahan karat. Hanya apabila kekuatan keluli tahan karat tidak mencukupi, pengikat bersalut krom digunakan.
Untuk mengelakkan kakisan, tembaga dan nikel perlu dilapisi terlebih dahulu sebelum penyaduran krom. Lapisan kromium boleh menahan suhu tinggi 1200 darjah Fahrenheit (650 ℃). Tetapi terdapat juga masalah pelengkap hidrogen, sama dengan electrogalvanizing.
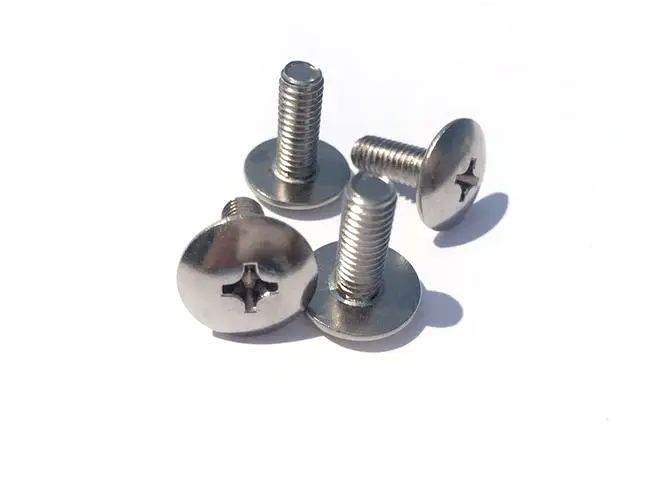
6. Nikel Plating
Terutamanya digunakan di kawasan yang memerlukan kedua-dua karat dan kekonduksian yang baik. Sebagai contoh, terminal keluar bateri kenderaan.
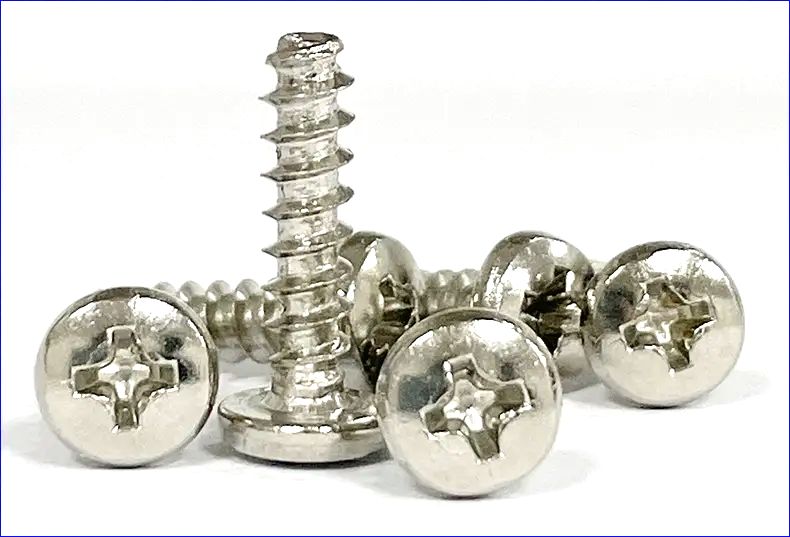
7. Galvanizing Hot-Dip
Hot Dip Galvanizing adalah salutan penyebaran haba zink yang dipanaskan kepada cecair. Ketebalan salutan antara 15 dan 100 μ m. Dan ia tidak mudah dikawal, tetapi mempunyai rintangan kakisan yang baik dan sering digunakan dalam kejuruteraan. Semasa proses galvanizing panas, terdapat pencemaran yang teruk, termasuk sisa zink dan wap zink.
Oleh kerana salutan tebal, ia telah menyebabkan kesukaran dalam mengacaukan benang dalaman dan luaran dalam pengikat. Oleh kerana suhu pemprosesan galvanizing panas, ia tidak boleh digunakan untuk pengikat di atas gred 10.9 (340 ~ 500 ℃).
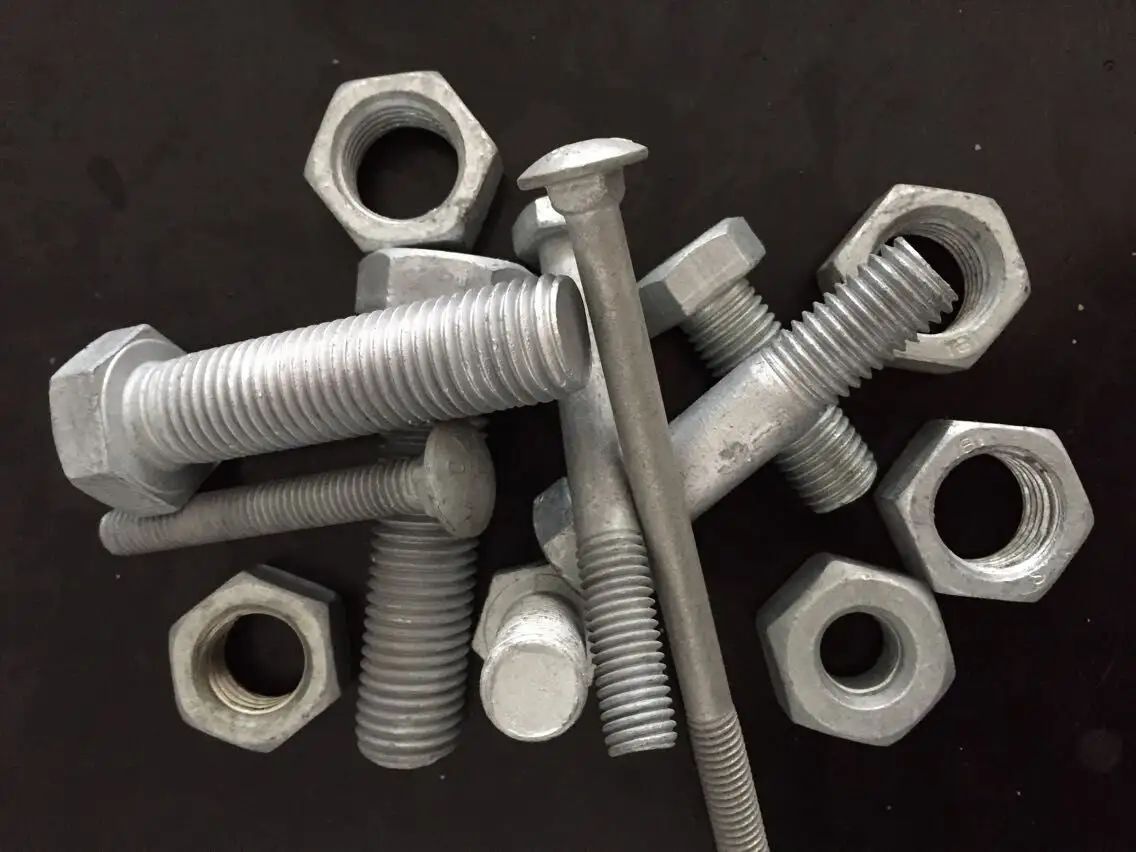
8. Penyusupan Zink
Penyusupan zink adalah salutan penyebaran haba metalurgi yang kukuh dari serbuk zink. Keseragamannya adalah baik, dan lapisan seragam boleh diperolehi dalam kedua -dua benang dan lubang buta. Ketebalan penyaduran adalah 10-110 μ m. Dan kesilapan boleh dikawal pada 10%. Kekuatan ikatan dan prestasi anti-karat dengan substrat adalah yang terbaik dalam lapisan zink (seperti electrogalvanizing, galvanizing panas, dan dacromet). Proses pemprosesannya adalah bebas pencemaran dan yang paling mesra alam.
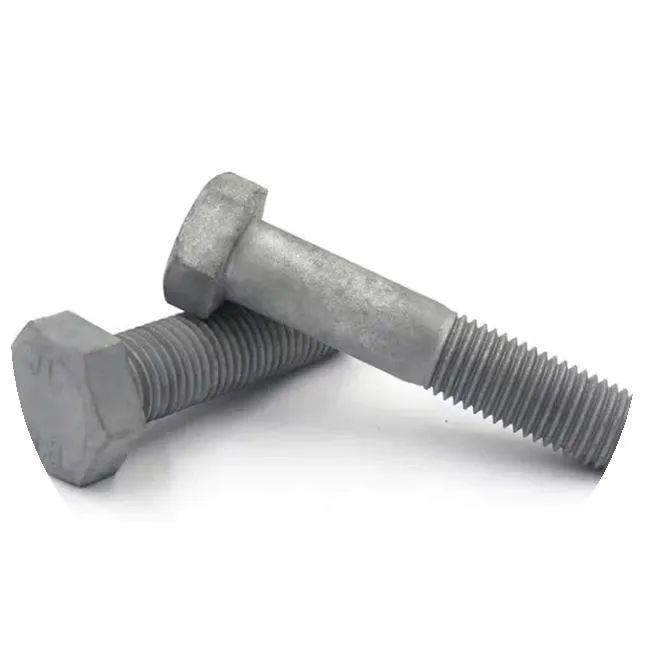
9. Dacromet
Tidak ada masalah pelupusan hidrogen, dan prestasi konsistensi preload tork sangat baik. Tanpa mempertimbangkan isu kromium dan alam sekitar, dacromet sebenarnya yang paling sesuai untuk pengikat kekuatan tinggi dengan keperluan anti-karat yang tinggi.
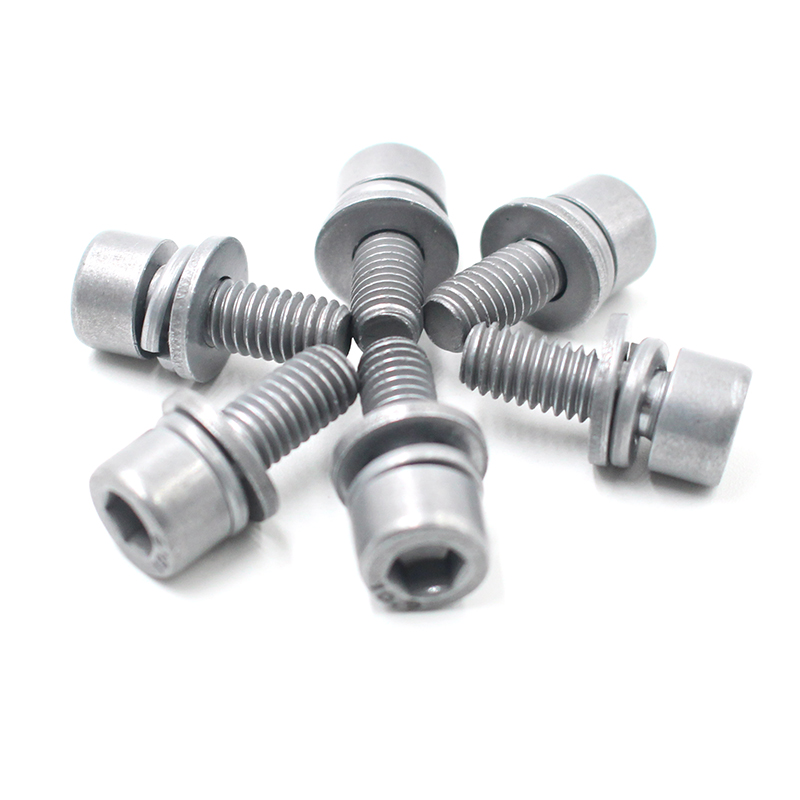
Masa Post: Mei-19-2023